“Showstopper” training hub latest addition to Prologis RFI DIRFT Phase III
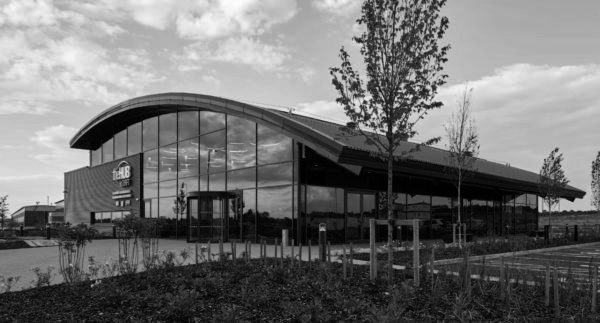
Stephen George + Partners LLP (SGP) is celebrating the completion of a “showstopper” 9,551 sqft training and education facility at Prologis RFI DIRFT – the UK’s largest rail-served logistics park, near Daventry.
Richard Smyth Partner at SGP: “We designed The Hub in close consultation with Prologis, who was a very hands-on and open-minded client. They wanted a showstopper building with a civic feel, that would set a high tone for the entire development and act as a catalyst for the design of amenities at other parks. Built in the same phase as the rail freight terminal, this wasn’t an after-thought, but an integral part of the development’s infrastructure.”
The Hub, as the building is known, is a dedicated centre for logistics training and education that can be used by occupiers at DIRFT. It is also home to the Prologis Warehouse and Logistics Training Programme – an initiative aimed at training those leaving education and re-skilling the unemployed by equipping them with the knowledge needed to pursue a career in logistics.
Tariq Khan Associate at SGP and Lead Architect explains: “The form of the building is the first clue as to the ambition of the project. Its arresting shape, a juxtaposition of arcing roof and linear box element, is both fluid and dynamic. The barrel roof is reminiscent of the roofs of the huge warehouses on site, and a full height glazed façade, designed specifically at Prologis’ request, connects the building to the main road access, presenting a transparent, inviting and active frontage to anyone entering the park”.
Explains SGP Interior Designer, Jess Puttock: “The building has three distinct areas, a reception and café, three flexible training rooms and three smaller meeting rooms, but we did not want it to feel like three separate parts. Although The Hub has a civic scale, we wanted to link back to techniques and methods used in construction of the warehouse units on park, delivering a “peeled back” approach that showed the bones of the structure and the honesty of the materials. We took the industrial feel and mixed it with biophilic elements, making the green elements – either planting or material effects – feel like they’ve been here a long time.”
Prologis did not want the reception and café area to look either like a hotel lobby or a traditional training centre, so the designers created a relaxed, student friendly but practical space, playing with the idea of freight and travel without over-stating the concept. The moss design wall covering that overhangs the reception desk follows the biophilia theme but the desk itself is made from corrugated metal reminiscent of shipping containers. A circular form of ring lights sits above the linear reception desk and the café area sits within a rectangular space dominated by vast rectangular glazing panels.
On the far wall is the first suggestion of the idea that the greenery is encroaching; a soft mottled green fades as it climbs higher, like the patina on aging metal or wild plants taking over. The intention takes physical form with the inclusion of many planters, including a statement circular planter with encircling seating. Soft natural materials are positioned against greys, blush tones, and browns, with shades of green used to make the other elements sing.
The large training rooms are designed as flexible spaces that can be three separate teaching areas or opened up into one single room for conferences or other large scale events. The design continues the stripped back idea and the links with freight in using level access doors to split some of spaces and allow access for large equipment from outside. Practicality was important. The design uses concrete flooring so large piece of equipment can be moved without damaging the surface and flip-top desks are easy to move aside when the space needs to be cleared. The colour scheme is mainly monochrome but slight hits of orange. A sparce, high-level, wall covering design of cogs playfully echoes the mechanics of trains and brains.
The three smaller meeting rooms continue with the concepts of journey and power, most obviously in the room names: Power room, Engine room and Connectivity. An abstract design of the power lines of a modern train control map / electrical circuit diagram, has been used along the walls, dropping down as if from the ducting, and across glazing elements such as meeting room doors, connecting the rooms with a sustained thread. The Engine room is a large board room which has a synergy with the reception area, seen in the corrugated metal wall covering, softened by a gentle teal finish. As in a real engine room, the parts are not hidden away. Ceiling lights are held in a ring doughnut configuration to avoid the necessity of a suspended ceiling and allowing clear views upwards to the structure and the full height glazing windows. Except for a striking zig-zag light fitting that echoes the linear feel of train or power lines, the Power room is currently a blank canvass, with the expectation that the interior will develop as it is used.
The designers’ eye for detail and commitment to the design concepts does not falter in the connecting spaces. The meeting room corridor continues the idea of showing off the structure of building by using a dark grey colour in the floor to ceiling window recesses to highlight the window cross bracing and lead eye upwards towards the visible roof structure. The area also continues the motif of creeping greenery with blocks of soft lime green in the flooring.
Continues Tariq: “The Hub has a strong emphasis on sustainability. The building specification applies a range of sustainable thinking, from sustainably sourced materials in line with our Sustainable Procurement Plan to lighter colours on external finishes to reflect thermal radiation and help avoid overheating. 10 EV charging points have been installed in the car park. We’ve achieved CO2 savings by installing carbon saving technologies including PV and solar thermal. These have the potential to save 16.5% (PV) and 6.2% (solar thermal) of total CO2 emissions based on Yonder’s LZC study.”
The Hub’s window-to-wall ratios ensure good daylighting values for the development and reduce the need for artificial lighting, which is of an energy efficient type. Openable windows allow for natural ventilation whilst maximum water efficiency credits are achieved from efficient sanitary ware fittings and an external underground rainwater harvesting tank.
The Hub is targeting a BREEAM Excellent rating.
As with all Prologis logistics parks, the external amenity spaces are as important as the internal rooms, offering additional sensory engagement and stimulating feelings of connection and well-being. The Hub is surrounded by hard and soft landscaping with seating that allows people to spill out for breakout sessions or relaxation. The landscaping forms, materials and colours mirror those used inside, with the anthracite grey seen in the interiors taken outside. Formal borders and trees with linear pathways and seating are set against the backdrop of the powerful curved roofline, harking back to the relationship between lines and curves. An overhanging canopy swoops down with great panache to allow rain from part of roof to fall unchecked into a French drain topped with outsized pebbles. Staff and students can sit in the dry space underneath and listen to the rain and watch the drops falling and splashing on the stones.
The Hub is a BIM level 2 project, designed in 3D from conception to completion. SGP was able to use its in-house VR system to help the client visualise every element of the design, from the muscularity of the exposed internal structure to water falling from the canopy overhang.
Explains Jess: “The interior design and build teams have been able to work together right from the beginning, understanding each other’s concerns and aspirations for the completed project. This strong collaboration – between front end, delivery and fit-out – meant that we could design the complete building and ensure all aspects were realised.”
Concludes Tariq: “SGP worked in close collaboration with the project team in order to achieve the high level of specification demanded by Prologis. We were able to combine experience and technical knowledge from across the practice to ensure that the Hub is the quality, showstopping building the client envisaged.”
Practical completion was in July and the building is now in use.
- X
- Share on LinkedIn
- Copy link Copied to clipboard
Read more from…
New extension for UK’s leading food wholesalers and suppliers
Start on Site for latest unit at Panattoni Park Sittingbourne
Ground-breaking ceremony marks commencement of final phase of popular Derby business park
SGP Celebrates Emerging Talent at Loughborough University’s End of Year Show
SGP celebrates trio of internal promotions
Celebrating 55 Years: SGP’s Annual Conference at The Hub
No related items found.